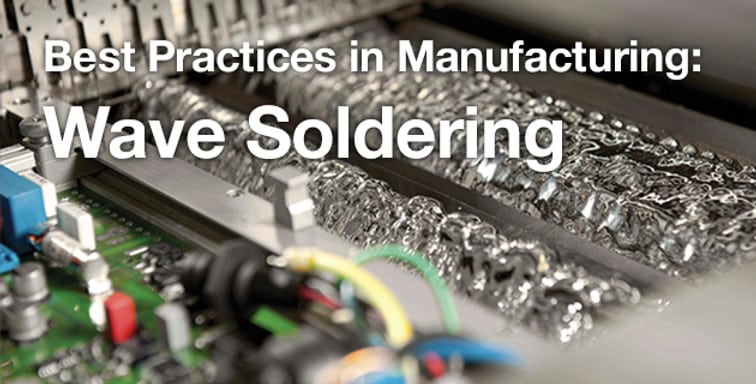
Mejores prácticas de fabricación: Soldadura por ola
A lo largo de los años, las mejores prácticas han evolucionado y seguirán evolucionando con los entornos cambiantes, las necesidades de las empresas y los retos, y lo que puede funcionar para una empresa puede no ser necesariamente lo mejor para otra. Un área común que a veces se pasa por alto en comparación con el montaje en superficie es la soldadura por ola, que normalmente puede introducir importantes retoques y retrabajos si no se gestiona adecuadamente.
Las siguientes recomendaciones se basan en la experiencia y en las mejores prácticas y no pretenden considerarse reglas rígidas, sino más bien directrices: su situación dictará qué prácticas funcionan mejor para su empresa.
Este artículo se centrará en los defectos comunes de las olas y en las mejores prácticas para abordar, predecir y prevenir proactivamente la reaparición de estos problemas. Se analizarán elementos que contribuyen a ello, como la selección y las consideraciones de los componentes, el diseño, las herramientas y el proceso.
El defecto de onda más común es, con mucho, el puenteo, que es la formación no deseada de soldadura entre conductores. Entre los factores que contribuyen a los defectos se encuentran los componentes, el diseño, las herramientas y el proceso.
Puente de soldadura
Consideraciones sobre los componentes
Longitud del cable - La especificación de la longitud del cable del componente en el diseño frente al grosor de la placa de circuito impreso proporciona la protuberancia respectiva del cable en la soldadura durante este proceso. Asegurarse de que la longitud del cable no es demasiado corta (es decir, la soldadura no puede llegar a la clavija para conseguir una acción capacitadora) ni demasiado larga (es decir, proporciona una vía para la transmisión de una clavija a la adyacente) puede favorecer la formación de puentes en el montaje.
La mejor práctica a la hora de especificar la longitud del cable del componente es asegurarse de que la longitud del cable es lo suficientemente larga como para proporcionar la transferencia de calor necesaria para una absorción adecuada que proporcione un llenado suficiente del barril, sin exceder la protuberancia máxima especificada según la norma IPC-A-610. Una buena regla general es que la longitud no debe ser mayor que la distancia entre los dos anillos anulares adyacentes. Si se cumple esta regla, se reduce significativamente la probabilidad de que se forme una red, ya que la tensión superficial atraerá la soldadura hacia la zona de cobre más cercana.
En los casos en los que la longitud del cable es demasiado larga, se recomienda preparar los componentes y recortar el cable para obtener la longitud deseada.

Figura 1: La altura de los componentes de montaje superficial en la parte inferior puede hacer que los requisitos de las paletas sean más gruesos y afectar aún más a la capacidad de la soldadura para fluir dentro y fuera de la cavidad.
Otras consideraciones relacionadas con los propios componentes pueden ser la contaminación por PCB, la contaminación de los componentes, la oxidación o los problemas de máscara de soldadura.
Consideraciones sobre el diseño
Orientación de los componentes - Especialmente relevante para los conectores de mayor número de pines con al menos 2 o más filas, en los que la orientación del conector paralela a la onda puede dar lugar a importantes ocurrencias de puenteo.
La mejor práctica a tener en cuenta es asegurar que los conectores de mayor número de pines estén orientados perpendicularmente a la onda para minimizar el número de pines expuestos en el extremo inferior del conector, donde es probable que se produzcan puentes. Esto es especialmente cierto para el paso fino. En situaciones en las que la orientación no puede acomodarse, pueden diseñarse otros métodos, como los ladrones de soldadura (almohadillas no funcionales o elementos de cobre que se colocan en el borde de salida para alejar la soldadura del último conductor y evitar el puenteo), bien en la placa o en la paleta de onda selectiva, para minimizar el puenteo.
Consideraciones sobre las herramientas
Algunas de las mejores prácticas en el diseño de la paleta de soldadura selectiva incluyen la orientación adecuada de la PCB en la paleta de onda selectiva. Se recomienda inclinar la placa entre 15 y 30 grados puede ayudar a mitigar el puenteo a unos pocos pines asegurando que sólo un puñado de pines terminen como pines de arrastre. Esto es especialmente útil cuando los conectores de pines más grandes están diseñados en paralelo a la dirección de la onda.
Unas aberturas de onda suficientemente grandes y unos canales de flujo de soldadura en la parte inferior de la paleta de onda proporcionan un flujo de soldadura y una aplicación de fundente suficientes que evitan la formación de charcos o zonas en las que la soldadura queda atrapada, lo que da lugar a la formación de puentes. Por lo general, las restricciones como la distancia mínima desde el borde exterior del anillo anular a una almohadilla de montaje superficial determinan el tamaño de la abertura. Se recomienda una distancia de 0,100" para un diseño adecuado.
La altura de los componentes de montaje en superficie de la parte inferior puede hacer que los requisitos de las paletas sean más gruesos y afectar aún más a la capacidad de la soldadura para fluir dentro y fuera de la cavidad. La relación de aspecto está relacionada con la longitud/anchura de la abertura de soldadura frente al recorrido vertical necesario para que la soldadura llegue a la parte inferior de la placa de circuito impreso. La relación mínima es de 1:1 para la soldadura con plomo, pero aumenta a 1:3 para la soldadura sin plomo. Es decir, si la longitud/anchura es de 0,150", la dimensión vertical máxima es de 0,150", para la soldadura con plomo. La violación de esta relación de aspecto obstruirá el flujo adecuado y aumentará la posibilidad de defectos relacionados con la onda.
Además, orientar la placa en la paleta de onda selectiva a 15 grados puede ayudar a mitigar el puenteo a unos pocos pines, normalmente una solución híbrida de las técnicas anteriores proporciona la solución óptima.
Consideraciones sobre el proceso
La selección del fundente adecuado para la aplicación, así como el perfil térmico apropiado, puede tener un impacto significativo en la formación de puentes de soldadura y la selección de un fundente apropiado para la masa térmica y el perfil de calentamiento requeridos puede tener un impacto significativo en el rendimiento general.
Por lo general, un contenido sólido más alto es más robusto a temperaturas más altas y los fundentes a base de agua no funcionan tan bien a temperaturas más altas y son más adecuados para placas de baja temperatura. Asegurarse de que la temperatura de precalentamiento y el tiempo de permanencia de su placa son adecuados para su fundente puede significar la diferencia entre un buen y un mal resultado. Quemar el fundente antes de la ola puede dar lugar a la formación de puentes.
Componentes elevados
Otro defecto común es el levantamiento de componentes después de la ola, que es más predominante en los componentes más pequeños, como los axiales o radiales (pero igual de común en los conectores y otros componentes) que se levantan durante el contacto con la ola y se sueldan en la colocación. La práctica más común para abordar es a través de la preformación del plomo del componente y / o la sujeción de la paleta.
Consideraciones sobre los componentes
Asegurarse de que los componentes, como los axiales y radiales, se preparan adecuadamente puede evitar la mayoría de las situaciones de elevación. La formación de los cables o el pinzamiento de los cables que mantienen mecánicamente los componentes en su lugar son, con mucho, los más comunes. Los cables demasiado largos también pueden exagerar el levantamiento, que actúa como una palanca para empujar el componente fuera de su posición.
Consideraciones sobre las herramientas
Otros componentes, como los conectores, que no pueden retenerse fácilmente en su sitio, requieren sujeciones adicionales, que pueden ser en forma de pegamento o abrazaderas como parte de la soldadura selectiva.
Al considerar los sobrebrazos para la sujeción, la masa térmica adicional introducida por estas características y debe ser considerada en el perfil y puede requerir potencialmente un flujo diferente para un mejor rendimiento.
Consideraciones sobre el proceso
La altura de las olas y el uso del flujo lambda frente al laminar también pueden contribuir a aumentar los casos de elevación de componentes. Hay que asegurarse de que la altura de las olas no supere el 50% del grosor de la placa de circuito impreso en relación con el palé y que se minimice el uso de flujos turbulentos.
Otras consideraciones son la vibración del transportador, el ángulo, etc.
Soldadura insuficiente
Otro de los defectos más comunes de la ola es la soldadura insuficiente y puede clasificarse como relleno incompleto del barril o humectación circunferencial incompleta.
La deshumectación o la falta de humectación están relacionadas con la contaminación de la soldadura, la placa o el componente. Para el propósito de esta revisión, supondremos que los componentes están en buenas condiciones antes del procesamiento. Las mejores prácticas para evitar la introducción de este tipo de defectos incluyen un proceso de inspección de entrada bien establecido, combinado con una prueba de inmersión de la soldadura según la norma IPC-TM-650 para los componentes sospechosos de estar contaminados u oxidados.
Consideraciones sobre el diseño
Las consideraciones de diseño más comunes son la conexión directa de los agujeros pasantes chapados con grandes planos de cobre que actúan como disipadores de calor durante la soldadura por ola. Para solucionarlo, la mejor práctica es proporcionar alivio térmico en estas áreas para permitir un flujo adecuado durante la soldadura. Los radios térmicos proporcionan aislamiento y pueden aumentar significativamente la probabilidad de una buena unión.

Figura 2: La conexión directa de los agujeros pasantes chapados con grandes planos de cobre actúa como disipador de calor durante la soldadura por ola. La mejor práctica es proporcionar alivio térmico en estas áreas para permitir un flujo adecuado durante la soldadura.
Otras consideraciones son los desajustes entre el diámetro del cable del componente y el diámetro del agujero pasante chapado. Un orificio pasante chapado que sea demasiado grande o demasiado pequeño en comparación con el cable puede resultar igualmente insuficiente. La relación de aspecto recomendada suele ser 0,6 más grande que el cable del componente para obtener buenos resultados.
Consideraciones sobre el proceso
Por lo general, esto se debe a la transferencia de calor o a la insuficiencia de fundente, ya que ambos pueden tener un impacto igualmente significativo en el relleno de la soldadura. La falta de penetración del fundente o la presencia de perfiles demasiado calientes son las causas más comunes.
Productos como los fluxómetros, que utilizan papel ácido y placas de circuito impreso especialmente diseñadas con agujeros pasantes regularmente espaciados, pueden utilizarse para garantizar que se aplique la cantidad de fundente y la penetración (es decir, la presión) adecuadas para un uso óptimo.
Las revisiones periódicas o mensuales, incluyendo las comprobaciones de nivel o los "wave riders", también pueden proporcionar una indicación del nivel de onda, el perfil de temperatura y el rendimiento general del horno, y se recomienda para garantizar que la desviación del proceso relacionada con el equipo no contribuya a los defectos.

Figura 3: Se puede utilizar un fluxómetro para garantizar que se aplica la cantidad adecuada de fundente y penetración para un uso óptimo.
Vacíos de soldadura
Los vacíos de soldadura o la desgasificación (agujeros de soplado y agujeros de clavija) se producen cuando una unión de soldadura tiene un pequeño agujero que penetra en la superficie de la conexión de soldadura. Esto se debe normalmente a la humedad atrapada que, durante el proceso de soldadura, expulsa los gases de la unión.
Consideraciones sobre el proceso
Al igual que los componentes, las placas de circuitos impresos también son sensibles a la humedad, pero no suelen tratarse de la misma manera que los componentes sensibles a la humedad. Como norma general, todas las placas de circuito impreso deben considerarse MSL 3 y gestionarse como cualquier otro dispositivo sensible a la humedad.
Best Practice is to ensure PCBs are sealed and only opened just prior to use. Extended periods between thermal cycle operations like surface mount reflow and wave should be considered when reviewing exposure time. If a board is not soldered within 72 hours after the previous thermal cycle operation, it should be baked to remove excessive moisture in accordance with J-STD-033 or kept in a dry cabinet with a relative humidity <5% to minimize the risk of such occurrences.
Bolas de soldadura
Los defectos de bolas de soldadura y salpicaduras se producen generalmente cuando una pequeña esfera de soldadura se adhiere al laminado, la resistencia o el conductor después de la soldadura por ola. Suelen ser de tres tipos: aleatorias, no aleatorias y salpicaduras, todas ellas relacionadas con el proceso.
Consideraciones sobre el proceso
En el caso de las bolas de soldadura aleatorias, éstas son las más fáciles de solucionar y suelen ser el resultado de un exceso de fundente antes de la ola, o de una altura de ola desigual. Si escucha un "chisporroteo" mientras la placa pasa por la ola de soldadura es una buena indicación de que el precalentamiento es demasiado bajo o la aplicación de fundente es demasiado alta o la temperatura de la ola está ajustada demasiado alta.
En el caso de las bolas de soldadura no aleatorias, en las que las bolas aparecen en el mismo lugar o en el pasador de arrastre, esto se debe normalmente a que el fundente es insuficiente o a que los precalentamientos son demasiado altos.
En el caso de las salpicaduras, esto se debe normalmente a que la altura de la ola es demasiado alta o a una turbulencia excesiva en la ola. El 95% de las aplicaciones, si se diseñan adecuadamente, se pueden soldar con flujo laminar solamente y se recomienda para ayudar a evitar ocurrencias.
La mejor práctica es utilizar herramientas como el Fluxómetro y el Waverider para comprobar el paralelismo y la optimización adecuada del flujo para minimizar estos casos.
Consideraciones sobre las herramientas
La revisión de los diseños de las paletas para el flujo de la soldadura para asegurar que hay suficientes canales de flujo o respiraderos para permitir la desgasificación durante la soldadura puede ayudar a minimizar la aparición de bolas de soldadura y salpicaduras.
Carámbanos, banderas y exceso de soldadura
Los carámbanos y las banderas (cuernos) y el exceso de soldadura se producen cuando una placa de circuito impreso que pasa por un proceso de soldadura acumula demasiada soldadura o desarrolla una protuberancia indeseable de soldadura en la unión. El factor más común es el proceso.
Consideraciones sobre el proceso
La razón más común es que la temperatura del crisol de soldadura por ola es demasiado baja o que el tiempo de permanencia en el crisol es insuficiente. Se recomienda un tiempo de permanencia de 3 a 5 segundos para una correcta formación de la unión. Herramientas como los Oven-riders pueden proporcionar una indicación de que se está produciendo una desviación de la temperatura del crisol de soldadura, pero siempre se recomienda medir la temperatura del crisol de soldadura con regularidad para asegurar la temperatura adecuada. Las lecturas de temperatura del crisol de soldadura de la máquina no siempre se corresponden con las reales y deben ser controladas.
La mejor forma de prevenir los defectos es aplicar las mejores prácticas mediante revisiones formalizadas del diseño y la aplicación de controles de proceso en torno a parámetros clave de la ola, como la temperatura del crisol de soldadura, el precalentamiento, la permanencia, el paralelismo y la optimización del fundente.
Actividades como el diseño para la fabricación (DFM ) o el diseño para el ensamblaje (DFA) pueden ahorrar mucho tiempo en la aplicación de las reglas de diseño para garantizar que las consideraciones de diseño de las placas de circuito impreso, los requisitos térmicos, la compatibilidad de la fabricación y los contribuyentes relacionados se identifiquen en las primeras fases del ciclo de diseño, donde los cambios pueden aplicarse a una fracción del coste.
Es importante alinearse con los socios estratégicos de fabricación desde el principio para proporcionar información relevante sobre todos los aspectos del diseño, ya que las decisiones de diseño tomadas desde el principio pueden afectar a la viabilidad y el coste del producto a largo plazo para el ciclo de vida total.
Para obtener más información sobre las mejores prácticas en la fabricación de productos electrónicos, póngase en contacto con VEXOS hoy mismo o llame al 855-711-3227
Vexos, es una empresa global de tamaño medio de servicios de fabricación de productos electrónicos (EMS) y soluciones de materiales a medida (CMS), que proporciona soluciones completas de gestión de la cadena de suministro de extremo a extremo en productos electrónicos y mecánicos para fabricantes de equipos originales (OEM) y nuevas empresas de tecnología emergentes.
Los servicios de Vexos abarcan todo el ciclo de vida de los productos electrónicos, desde los servicios de ingeniería de valor para el desarrollo de productos hasta la creación de prototipos y la introducción de nuevos productos (NPI), pasando por las fases de crecimiento, madurez y fin de vida, con un fuerte enfoque y compromiso con la calidad y la satisfacción del servicio al cliente.
Con instalaciones en Estados Unidos, Canadá y China, Vexos puede competir eficazmente en el mercado actual, centrándose principalmente en los segmentos de mercado de la automoción, la industria, las redes, las comunicaciones, la medicina y la seguridad. Vexos permite a sus clientes centrarse en su negocio principal, reducir sus costes, acelerar su tiempo de comercialización y obtener una ventaja competitiva.
Brain Morrison, vicepresidente de ingeniería de Vexos, es el responsable directo del proceso, las pruebas y el desarrollo, centrado en la introducción de nuevos clientes y nuevos productos. Morrison ayudó a desarrollar la hoja de ruta tecnológica corporativa de la empresa, los sistemas y procesos, la ingeniería de valor, la gestión medioambiental y las iniciativas de fabricación para impulsar un coste más bajo, soluciones flexibles e innovación en la fabricación.