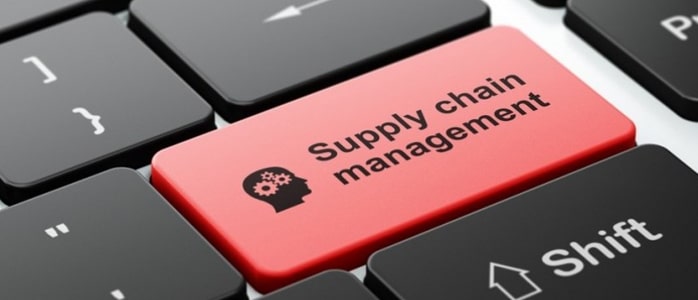
Retos del suministro de componentes desde el asiento del pájaro
Entrevista con el equipo editorial de I-Connect007.
Stephanie Martin, Vicepresidenta Senior de Suministros Globales de Vexos, ofrece al equipo editorial de I-Connect007 una visión amplia y perspicaz de la situación actual del suministro de piezas desde la perspectiva de las compras en un fabricante por contrato.
Stephen Las Marias: En primer lugar, Stephanie, ¿puedes hablarnos más de Vexos y de tu papel en la empresa?
Stephanie Martin: Sí. Soy la vicepresidenta senior de suministro global de Vexos.
Vexos es un fabricante por contrato de nivel 3 alto y nivel 2 bajo. Es una combinación de dos empresas diferentes que fueron adquiridas por Center Lane Partners, una empresa de capital riesgo: EPM, con sede en Markham (Canadá), y STACI Corporation, con sede en LaGrange (Ohio).
Tenemos cinco plantas de fabricación por contrato. Tenemos la planta de Markham(Canadá), que se centra más en la alta tecnología y el paso fino. Luego tenemos la planta de LaGrange(Ohio), en la zona de Cleveland, que fabrica productos médicos, de automoción y de baja tecnología. Tenemos dos instalaciones en China: una en Shenzhen, que suele coincidir con lo que hace Markham -más paso fino y productos de alta tecnología- y otra en Dongguan, que se dedica a la automoción, la medicina, muchos productos de baja tecnología y otros tipos de fabricación que no se basan en la electrónica y, por último, tenemos Vietnam, que se encuentra en la ciudad de Ho Chi Minh, nuestra instalación de fabricación más reciente, inaugurada en mayo de 2019, que ofrece a nuestros clientes una solución de fabricación alternativa de bajo coste.
Además, tenemos otra parte de nuestro negocio que llamamos "solución de material a medida". Somos una empresa comercial y representamos a una serie de socios proveedores de productos a medida como placas de circuito impreso, conjuntos de cables, pantallas, disipadores térmicos, piezas metálicas fabricadas, piezas metálicas para maquinaria y moldeo por inyección de plástico. Creemos que somos la única empresa de nivel 3 en nuestro sector que ofrece no sólo una solución global, sino una gama completa de componentes que podemos suministrar desde la carcasa exterior, independientemente de que usted realice o no el montaje electrónico. Podemos suministrarle desde las placas de circuito impreso hasta la caja completa.
Las Marías: Desde su punto de vista como proveedor de SME, ¿cuáles son los mayores retos a los que se enfrenta o que experimenta en lo que respecta a la cadena de suministro?
Martin: Bueno, estamos en el super-ciclo para la asignación, por lo que estamos fuertemente en el super-ciclo que estamos tratando. Comenzó con el producto de memoria, que estamos llegando a tres años ahora. Y luego, en el verano de 2017, los MLCC empezaron a escasear. En noviembre, estábamos en plena asignación de placas. Luchamos como todas las empresas de EMS, especialmente con los MLCC. Los plazos de entrega son de más de 52 semanas con la mayoría de los fabricantes, si es que aceptan pedidos.
Los fabricantes de MLCC de segundo y tercer nivel ya no cruzan sus componentes, y para los distribuidores, la posición de inventario es baja. Así que cada vez que recibimos un pedido, encontrar los MLCC es todo un reto. También estamos viendo cambios en el tantalio. Muchos de ellos se están asignando ahora. Tenemos MOFSETs en todo el tablero que se están ejecutando en la asignación de toda la placa durante 40 semanas. Luego tenemos los IGBT y los diodos TV, Zener y Schottky, todos ellos en el rango de las 38 semanas.
En el campo de las resistencias, la serie CRCW de Vishay cuenta ya con 80 semanas. La serie ERJ de Panasonic tiene más de 40 semanas. En general, los principales fabricantes de resistencias tienen entre 26 y 29 semanas. Se ha convertido en todo un reto abastecerse de componentes electrónicos. Dedicamos mucho tiempo a hablar y trabajar con nuestros clientes para que aprueben rápidamente alternativas que nos permitan encontrar materiales y ampliar su AVL, y dedicamos mucho tiempo adicional al aprovisionamiento para encontrar inventario. Se ha convertido en todo un reto en este mercado.
Las Marías: Ha mencionado el superciclo. ¿Ha experimentado antes este tipo de escasez extrema en el suministro de componentes electrónicos?
Martin: Llevo en la electrónica desde 1989, así que llevo mucho tiempo. He pasado por varios ciclos. Creo que este es el décimo ciclo de inventario que estamos en lo que puedo decir. Lo más cerca que hemos estado nunca, y la última vez que entramos en una situación de escasez que afectó a los componentes pasivos, fue en 1999, justo antes de la caída de las puntocom. En aquel momento, tuvimos problemas con resistencias y condensadores. Esa fue la última, y en mi carrera, la única vez que los productos pasivos han sido un problema.
Normalmente, el mercado sigue a un nuevo dispositivo imprescindible, ya sea un localizador, un teléfono móvil o un ordenador portátil. Este ciclo de mercado es muy diferente. No se trata de un único dispositivo. Este segmento de mercado es realmente lo que llamamos "la electrificación de todo". Se está produciendo un cambio enorme. Muchas partes de nuestra vida que nunca fueron electrónicas ahora están conectadas electrónicamente a nuestros teléfonos y dispositivos inteligentes. Incluso tenemos un cliente con el que estamos hablando que quiere que los filtros de la caldera sean inteligentes, para que te recuerden que tienes que cambiarlos.
Todos los dispositivos, incluyendo IoT, dispositivos inteligentes, contenido de automoción y teléfonos móviles nos están golpeando al mismo tiempo. Ningún dispositivo arreglará el mercado una vez que esté satisfecho. Lo único que creo que va a arreglar el mercado es que podamos aumentar la capacidad con la llegada de nuevos fabricantes. También se está produciendo un cambio tecnológico, que parece muy parecido al que se produjo a mediados de la década de 2000 con la directiva RoHS, cuando se pasó de las piezas con plomo a las piezas sin plomo.
Si nos fijamos en un condensador 1206, pueden caber aproximadamente 80 condensadores 0402 en el mismo espacio o 300 0201. Como el mercado está más ajustado, creo que los fabricantes de equipos originales se verán obligados a rediseñar piezas cada vez más pequeñas, y eso permitirá a los fabricantes producir más piezas en el mismo espacio que antes. Creo que eso es lo que va a ocurrir. Todas las proyecciones que recibimos de los fabricantes y del canal de distribución nos dicen que el mercado no verá un alivio hasta mediados de 2019 como muy pronto, y varios de ellos dicen que será hacia finales de 2019 para los MLCCS en particular Para los MLCC de mayor tamaño de carcasa puede que nunca se recuperen.
Están ocurriendo varias cosas. Los chinos están introduciendo nuevas fabricaciones. Varios fabricantes están recuperando parte de su fabricación interna, sobre todo en EE.UU. Algunos proveedores de tercer nivel están entrando y empezando, sobre todo en Asia. Están ocurriendo muchas cosas, pero el mercado tardará un tiempo en estabilizarse.
Dan Feinberg: Tengo que estar de acuerdo contigo en lo del superciclo. Es el mayor que he visto desde 1960-1962, cuando pasamos del cableado punto a punto a las placas de circuitos. La industria era mucho más pequeña y las demandas mucho menores y menos generalizadas. Algunas de las cosas que veo y oigo es que este superciclo puede durar bastante más que 2019 porque es una cuestión de oferta y demanda.
Con unos plazos tan largos, y usted ha respondido a parte de esto, ¿tiene previsto o espera que se incorporen nuevas instalaciones a lo largo de la cadena de suministro, y dónde? Con los problemas arancelarios que se avecinan, parece que esto va a ser más serio de lo que la gente pensaba o esperaba, al menos en esta industria. Aunque es probable que la economía estadounidense en general se beneficie de ello, esta industria puede o no beneficiarse. Podrían ser aranceles importantes y durar bastante tiempo. ¿Ha cambiado eso o ha cambiado dónde pueden producirse las expansiones que se han planeado?
Martin: Permítanme responder a eso en dos partes. La cuestión de los aranceles es un tema totalmente distinto que podemos discutir. Cuando me he reunido con varios fabricantes, he visitado las fábricas de Vishay y Yageo y varias otras en China y me he reunido directamente con los representantes de Murata, así que he tenido bastantes conversaciones. La sensación general que tengo es que las piezas más demandadas son las que antes llamábamos "piezas de palomitas de maíz", es decir, las piezas de bajo coste. Con el tiempo, desde la quiebra de las puntocom en 2000, los precios se han deprimido hasta el punto de que los márgenes para los fabricantes son muy bajos, lo que hace que su precio medio de venta no les resulte rentable.
Feinberg: No es atractivo para la expansión.
Martin: Sí, no es atractivo. Así que es poco probable que los fabricantes vengan a menos que sean de tercer nivel, lo que probablemente sería en China. Estamos viendo algunos de tercer nivel aparecen en China, aunque no nos citan. Dicen que ya están al máximo de su capacidad. Ninguno de los principales fabricantes con los que he hablado se está expandiendo en los tamaños de caja más grandes. Se están expandiendo en los tamaños 0201 y 1005, pero no en el 0402 y superiores. Ahí es donde sigue estando la mayor parte del sector industrial, en los tamaños más grandes. Creo que el único alivio real que va a llegar para esos tamaños de piezas es cuando los fabricantes de equipos originales decidan hacer un rediseño en los tamaños más pequeños.
Por lo que sé, estos tamaños más grandes, a partir del 0603, no tendrán más de tres o cinco años de vida útil. Cuando la industria del automóvil los elimine, creo que la mayoría habrán desaparecido, así que eso es lo que va a impulsar el cambio tecnológico. Nos han dicho que un automóvil actual tiene unos 3.000 MLCC, y un vehículo eléctrico tiene 30.000 MLCC. Cuando el mercado se ajuste a los tamaños más pequeños (0201 e inferiores), creo que empezaremos a ver un alivio y los pocos actores que queden podrán satisfacer la demanda de piezas de mayor tamaño. Pero, en los tamaños más grandes, no veo mucha capacidad nueva.
Lo que hacemos en ese sector es trabajar con nuestros clientes. Les hacemos análisis de la lista de materiales y les damos opciones para cruzar. Me reúno personalmente con muchos de ellos. Les animamos a rediseñar sus productos en función de su ciclo de vida, para garantizar la cobertura de las piezas al final de su vida útil. Murata anunció a principios de año el fin de la vida útil de muchas piezas; la última compra es en marzo del año que viene. Cuando eso ocurra en marzo, habrá una gran escasez, y creo que los plazos de entrega se alargarán más de lo que están hoy, cuando todos los clientes que no han actuado se den cuenta de que no van a conseguir esas piezas. Murata es la empresa más importante y tiene entre el 30 y el 40% de la cuota de mercado mundial. Otros fabricantes, como Kemet y AVX, ya nos han comunicado que no van a retirar esas piezas, pero que no pueden hacer frente a los requisitos adicionales que se les van a imponer. Por lo tanto, creo que habrá un problema importante a principios de año.
Feinberg: He tenido algunos indicios muy leves de que hay algunos fabricantes de equipos originales considerando la posibilidad de hacer lo que se hizo en los años 60 y 70 y empezar a hacer su propia fabricación y montaje. Es algo que han abandonado por completo. ¿Sabe de algún fabricante que se esté planteando hacer algo parecido?
Martin: Sí, hemos oído que algunos tiran de él en el lado de los semiconductores. Eso puede ayudar a componentes como los MOSFET, pero no a los MLCC. Hemos oído que un par de fabricantes están retirando algunos en casa en los EE.UU..
El otro problema es que los tres principales fabricantes de Taiwán sufren escasez de lingotes, por lo que tienen problemas de suministro. Acabo de leer una noticia sobre TSMC, el más grande, que puso una nueva máquina en línea. La máquina tenía un virus, y perdieron toda su tirada de obleas; retrasó las piezas de Zilinx hasta el cuarto trimestre de 2018. Creo que todo el mundo está tratando de pasar por el mismo tipo de análisis en los semiconductores para que puedan tirar de ellos de nuevo en casa, probablemente más fácil.
Cuando estuve allí, Yageo nos dijo que las resistencias están teniendo problemas con las materias primas, lo que puede deberse a los requisitos medioambientales que han impuesto los chinos. Han estado cerrando bastantes de sus proveedores debido a los requisitos de pureza del agua y del aire. Han tenido problemas con el metal, el papel y los sustratos que utilizan. Han tenido bastantes problemas para conseguir materias primas para las resistencias. Yageo es su mayor fabricante de resistencias, y Murata es su mayor fabricante de condensadores, por lo que hay niveles de problemas en la cadena de suministro a lo largo de todo el proceso. Hay problemas de materias primas y capacidad. Se están moviendo para apoyar las mayores necesidades de los conjuntos de automoción y portátiles. Han abandonado el sector industrial, y están ocurriendo muchas cosas al mismo tiempo.
Feinberg: Incluso hay una tremenda dificultad para conseguir laminado. Los plazos de entrega para la fabricación de placas de circuito impreso son muy largos.
Martin: Tuvimos ese problema el verano pasado, cuando no pudieron conseguir las láminas para fabricar los laminados porque iban destinados a baterías y vehículos eléctricos. Últimamente no hemos tenido muchos problemas de fabricación. La mayoría de nuestros proveedores chinos han vuelto a sus plazos de entrega normales, entre seis y ocho semanas. El verano pasado habían subido a más de 10 semanas, y los precios se dispararon. Los precios han vuelto a bajar y se han estabilizado un poco, y los plazos de entrega han bajado. La mayoría, al menos con nuestros proveedores, se han solucionado. Sin embargo, seguimos teniendo problemas con los pasivos, resistencias, condensadores y elementos discretos como MOSFETs, diodos y ese tipo de dispositivos. Eso es lo que nos está dando mucho trabajo.
Barry Matties: Algunas empresas se anticiparon a la escasez de condensadores y empezaron a almacenar a principios de 2017, tal vez incluso antes. De cara al futuro, ¿qué otras situaciones de escasez deberíamos tener en cuenta para hacer acopio de existencias?
Martin: Ahora mismo, lo siguiente son las resistencias y los MOSFET, que acaban de aparecer como verdaderos problemas (aparte de Vishay y Panasonic, que han sido un problema todo el tiempo). Creo que te estás fijando en los productos discretos. Sus plazos de entrega han aumentado mucho, como estamos empezando a ver. Hemos tenido bastantes problemas con los MOSFET. Pero creo que son problemas a corto plazo. No creo que vayan a ser un problema a largo plazo.
La cuestión de los aranceles ha empeorado aún más una situación que ya era mala. Hacemos un seguimiento de los aranceles porque somos globales y tenemos que lidiar con aranceles de todas las direcciones. Una de las cosas que descubrimos es que, dado que somos principalmente un cliente de distribución, todo el inventario de distribución se almacena en EE.UU. Incluso los distribuidores canadienses almacenan todos sus productos en EE.UU., lo que les hace estar sujetos a aranceles.
En nuestras instalaciones de China -porque tenemos clientes con sede en EE.UU.- hay precios especiales de fabricación que solo pueden obtenerse si los compramos a través de EE.UU. Tenemos algunos programas en los que todavía tenemos que comprar piezas fuera de EE.UU., que ahora están sujetas a los aranceles. La lista 1 incluye los electromecánicos y los LED, no los diodos, sino los LED. La lista 2 incluye prácticamente todos los componentes electrónicos, por lo que afecta a todos ellos. La lista 3 incluye la mayoría de PCBA, placas de circuito impreso en bruto y otras piezas utilizadas en productos electrónicos. A través del canal de distribución, están trabajando en estrategias de mitigación para Canadá, México y China, por lo que no tendrán los aranceles pasan a través. Tenemos tres formas principales en que los aranceles están llegando a nosotros. En este momento, sabemos de 14 fabricantes que son los importadores de registro y están incorporando el aumento de aranceles como un aumento de precios.
Hemos visto aumentos de precios en algunos componentes de hasta el 80%, así que están juntando el aumento de precios y el arancel. En algunos casos, los distribuidores son los importadores registrados. En la mayoría de los casos, lo están mitigando a través de una zona franca, un proceso de devolución de aranceles o utilizando un almacén en Guadalajara, dependiendo de quién sea el distribuidor. La última forma en que nos afectan los aranceles es que los fabricantes son los importadores registrados. Ellos facturan a los distribuidores, que nos facturan a nosotros. En ese caso, lo complicado es que los fabricantes que facturan lo hacen al coste contable, no al coste cargado o final.
Donde puedes tener un precio especial de 75 céntimos, el coste del libro es de 1 dólar. Vas a pagar el arancel sobre el dólar, no sobre los 75 céntimos, así que ahora mismo es un verdadero reto. Estamos registrando el arancel armonizado y los códigos HTS de todas las piezas. Pedimos el país de origen cuando hacemos un pedido. Y si tenemos la opción de utilizar un país de origen distinto de China, allí es donde vamos, incluso si el precio es un poco más alto.
Estamos oyendo que los fabricantes que ya tienen centros fuera de China están estudiando la posibilidad de reprogramar su negocio de bienes con sede en Norteamérica a centros fuera de China. No hemos visto mucho todavía, pero estamos escuchando que está sucediendo. En el caso de nuestras instalaciones en EE.UU., examinaremos muy detenidamente quiénes son los fabricantes y de dónde proceden. Si tenemos opciones para evitar este arancel del 25%, allá iremos.
Andy Shaughnessy: Mis lectores son principalmente diseñadores. Digamos que tienes un producto que saldrá en las próximas Navidades de 2019. Aparte de hacer acopio de existencias, ¿cómo planifican el futuro? ¿Qué deberían hacer para intentar adelantarse?
Martin: Cuando me reúno con los ingenieros, les digo que, si se trata de un producto nuevo, lo diseñen en el tamaño de caja más pequeño posible; 0201 y 0105 son su mejor opción. En esos casos, si puedes aprobar la calidad de automoción, tienes más posibilidades de conseguir piezas. Suelen ser un poco más caras, pero aún así se pueden conseguir piezas de calidad automovilística. Si no puedes diseñarlo, tienes que ofrecer tantas alternativas como sea posible. Lo peor que puedes hacer es salir con una pieza de un único proveedor, porque al final tendrás problemas con la cadena de suministro en algún momento, ya sea hoy o más adelante.
Lo que pedimos a nuestros clientes antes de que se estabilicen y mientras están en el proceso de diseño es que nos dejen analizar su lista de materiales. Utilizamos el software IHS Connect como modelador predictivo. Lo que nos gusta es trabajar con ellos cuando aún están en la fase beta. Si tienes un socio con el que vas a trabajar para subcontratar tu producto, tienes que darle la autoridad para hacer pedidos de piezas en cuanto las califiques, para que al menos puedas ponerte en marcha. Es más rentable pedir las piezas una vez que se han canalizado que empezar de cero y pedirlas esperando los plazos de entrega.
Alguien tiene que encargarlas. La realidad es que, a menos que se trate de piezas no cancelables ni retornables, puedes cancelar o reprogramar el pedido en un plazo de 45 días normalmente sin problemas. Si son algunas de las piezas realmente calientes, no tienes ninguna responsabilidad. Hay muchas estrategias que puedes seguir si tienes un diseño en camino, pero tienes que pensar con antelación en la planificación de la cadena de suministro.
Shaughnessy: Parece que sólo tienen que permanecer en la pelota.
Martin: No hay una fórmula mágica.
Las Marías: En lo que respecta a la cadena de suministro, uno de los problemas es la falsificación de componentes. Ahora que la industria se enfrenta a esta grave escasez, ¿espera que aumente el número de componentes falsificados en el mercado?
Martin: Por supuesto. Es una de las cosas de las que hablamos con los clientes. El mercado gris se está agotando. Varios fabricantes han cerrado la puerta trasera a los proveedores del mercado gris, los independientes. Además, algunos distribuidores han cerrado la puerta principal, por lo que no pueden hacer pedidos desde sus sitios. La cantidad de existencias que sigue disponible a través del mercado gris es cada vez menor, lo que significa que aumenta el riesgo de falsificación.
Tenemos un pequeño grupo de empresas independientes autorizadas que hemos auditado. Cada uno de ellos tiene laboratorios independientes con los que trabaja para comprobar la calidad. Los distribuidores exigen ahora que estén autorizados a hacer pruebas destructivas debido al alto riesgo de falsificación. Aún no hemos visto ningún material falsificado, pero somos muy cautos y estamos muy atentos.
Las Marías: ¿Qué puede aconsejar a nuestros lectores en relación con estas cuestiones en la cadena de suministro?
Martin: Tienen que hacer previsiones. Aunque no sea al 100%, necesitan previsiones continuas para 52 semanas. Entendemos que los clientes no tengan tanta visibilidad, pero tienen que dar a sus socios tanta visibilidad como sea posible. Un plazo de 52 semanas es bastante normal. Todas las listas de materiales tienen componentes de más de 40 semanas, cada una de ellas. Eso no significa que no podamos encontrar piezas, pero cuando el mercado gris, el inventario disponible y el canal de distribución se agoten, no habrá piezas. Te verás obligado a esperar. Los clientes que están en mejor situación hacen previsiones continuas. Las actualizan mensualmente a lo largo de 52 semanas.
Cuando su socio les da un componente alternativo, tienen que aprobarlo muy, muy rápidamente. Hoy en día, si está en el mercado gris, desaparece en 24-48 horas. Si el cliente tarda una semana en aprobarlo, el inventario desaparece. La próxima vez que lo encontremos, el precio puede haber subido. Yo les sugeriría que almacenaran los componentes críticos en stock y autorizaran un stock adicional en los componentes asignados. A continuación, estudien un rediseño para los tamaños de caja más pequeños. Si al ciclo de vida de su producto le quedan entre tres y cinco años, puede que quieran estudiar la posibilidad de dotarse de un colchón adicional para el final de la vida útil. Si el ciclo de vida de su producto es de ocho a diez años o más, entonces sí que deberían plantearse rediseñar las cajas pequeñas para que sean sostenibles.
Por último, tienen que buscar un tipo alternativo de materiales. En los MLCC, normalmente se puede sustituir la cerámica por chips de tántalo en una proporción de cuatro a uno. Aunque el tántalo presenta algunos problemas de plazo, no es tan malo como la cerámica, y existe una tecnología más reciente: el polímero. El polímero es una buena opción si ven que su producto es de 35 voltios o menos. Necesitan buscar potencialmente una tecnología diferente a la cerámica. En la resistencia de la serie CRCW de Vishay, si pueden utilizar el intervalo de temperatura no automovilístico, pueden añadir una C al final de la referencia y los plazos de entrega bajan de 80 semanas a aproximadamente 12 semanas. Hay muchas cosas que pueden hacer para mejorar.
Matties: ¿Hay otras estrategias que puedan utilizar los diseñadores? Ha mencionado el tamaño de las minúsculas, lo cual tiene sentido, pero ¿hay otras estrategias que los diseñadores puedan emplear para combatirlo?
Martin: Sí, si en general sólo buscan la producción a largo plazo, hay un enorme cambio tecnológico que se está produciendo ahora mismo. Estamos en las primeras fases. Creo que se va a acelerar y que la industria se va a hacer más pequeña. Por tanto, el diseñador debe utilizar las piezas más pequeñas que pueda. Los diseñadores tienden a utilizar las piezas con las que se sienten cómodos. No es raro que cuando vemos un nuevo diseño tenga componentes obsoletos.
Esa es una de las razones por las que sugerimos a nuestros clientes que nos dejen revisar su lista de componentes antes de finalizar el diseño. Podemos ofrecerles sugerencias sobre componentes alternativos con la misma forma, ajuste, función y colocación. Es diseñar para la cadena de suministro. Hay muchas cosas que tienen que tener en cuenta a la hora de diseñar para la cadena de suministro a largo plazo. Cada vez más dispositivos van a ser electrónicos, por lo que el propio mercado va a seguir expandiéndose, haciendo cada vez más difícil conseguir piezas más grandes. Eso es lo que yo diría a los diseñadores.
Matties: ¿Tienen también diseñadores en su lista de empleados y lo ofrecen como un servicio?
Martin: No, trabajamos con servicios externos si un cliente necesita diseño. Yo tengo ingeniería de componentes en mi plantilla. Hacemos un análisis del ciclo de vida del componente utilizando modelos predictivos, y lo hacemos en una escala del uno al cinco. Les digo a los diseñadores que, a menos que estén en la vanguardia de la tecnología, deben mantenerse alejados de las piezas del ciclo de vida uno. Son piezas nuevas y no están aceptadas en el mercado. Los precios son muy altos y hay muy pocos fabricantes.
Si se trata de un nuevo diseño, hay que buscar un ciclo de vida de dos a tres y medio en la curva. Un dos significa que está empezando a crecer, que hay más fabricantes, que los precios están bajando y que la oferta es mayor. El ciclo de vida tres es cuando hay más fabricantes. Está en su punto de precio más bajo, y te da la mayor oportunidad de la cadena de suministro. A partir del ciclo tres y medio o cuatro, las piezas disminuyen, los fabricantes abandonan el mercado y los precios suben. Y, por supuesto, cinco es obsoleto.
Si estás haciendo un nuevo diseño, en el análisis de la lista de materiales que hacemos para los clientes, les mostramos el ciclo de vida de las piezas y les decimos: "Tienes que conocer el ciclo de vida de tu artículo final. ¿Cuánto dura y cómo se corresponde con el ciclo de vida de los componentes?". Pero si estás en un nuevo diseño y buscas componentes que ya van hacia la fase de declive, tendrás problemas en la cadena de suministro.
Matties: Tienes razón. Los diseñadores deberían ser conscientes de ello desde el principio.
Martin: Según mi experiencia, la mayoría de los ingenieros están algo aislados de la cadena de suministro, por lo que realmente desconocen el ciclo de vida de esos componentes. Sin embargo, es probablemente el aspecto más crítico en un nuevo diseño para asegurarse de que tiene sostenibilidad en él.
Matties: ¿Cuántos diseñadores se ponen en contacto contigo para revisar la lista de materiales antes de hacer sus diseños?
Martin: Hemos sido muy agresivos con estas listas de materiales. Hacemos dos cosas para nuestros clientes, incluido un análisis de la salud de la lista de materiales, en el que hacemos el ciclo de vida de las piezas y les mostramos la situación de los MLCC. En esos MLCC, cruzo la lista de fin de vida de Murata con todos sus componentes por voltaje, microrreferencia y dieléctricos. Les decimos cuáles van a ser sus piezas problemáticas a largo plazo, y también hacemos un modelo de inventario y existencias de parachoques en el que nos basamos en los plazos de entrega del mercado.
Cuando hago esto con los clientes, se les abren los ojos. Los clientes con los que lo hemos hecho presionan mucho a sus equipos internos de diseño para que sean muy conscientes de lo que está pasando y se adelanten a los acontecimientos. Es eficaz cuando se hace.
Nolan Johnson: Desde tu punto de vista, ¿cómo recomendarías a los diseñadores que obtuvieran más información? Obviamente, una vez que están haciendo el análisis con usted en lo que ellos piensan que es su diseño terminado, cualquier problema puede hacer que tengan que volver atrás y hacer un rediseño completo. Esperemos que no sea tan grave, pero esa es la dinámica que se está estableciendo aquí. Si pueden tomar mejores decisiones en la herramienta de diseño y ofrecerte una lista de materiales y un diseño mejores con piezas actualizadas, ¿adónde deben dirigirse para ser eficaces?
Martin: La mayoría de los diseñadores recurren a los distribuidores. Ahí es donde obtienen las piezas de muestra y ese tipo de cosas. Deberían pedir a sus distribuidores los ciclos de vida porque ellos tienen esa información. Pueden utilizar un servicio de software. Hay dos: Silicon Experts e IHS Connect. Ambos son programas excelentes. Los propios distribuidores tienen esta información y deberían trabajar con su cadena de suministro si no la tienen.
Cuando trabajaba para los fabricantes de equipos originales, solía celebrar reuniones para almorzar y aprender. Traía a los distribuidores. Pero en este mundo, y con el cambio tecnológico que se está produciendo, tienen que adelantarse. No se trata de diseñar como siempre. Como he dicho, hay un enorme cambio tecnológico que se está acelerando. Si no conocen el ciclo de vida de los componentes, se enfrentarán a graves problemas en breve.
Feinberg: En primer lugar, permítame felicitarle. Es usted un gran conocedor de sus temas y está muy bien preparado. Es un placer mantener esta conversación con usted.
Martin: Gracias.
Feinberg: Desde el punto de vista del diseño, ¿se observa algún movimiento hacia la soldadura a baja temperatura que pueda provocar un alejamiento significativo de la soldadura por ola en su nivel de fabricación?
Martin: No puedo responder a esa pregunta. Tendría que preguntar a nuestros ingenieros. No soy ingeniero, sino especialista en la cadena de suministro, pero aún no lo he oído por aquí.
Feinberg: Si se entera de algo, por favor háganoslo saber. Es algo que estoy siguiendo y que me interesa.
Martin: Tenemos un gran jefe de ingeniería que puedo conectar con usted. Se llama Brian Morrison. Estoy seguro de que podría responderte; es muy técnico.
Feinberg: Nos encantaría tener esa oportunidad. El otro comentario que quiero hacer es sobre las previsiones. Una de las cosas que dificulta tanto las previsiones es que muchas empresas, los fabricantes de equipos originales, no siempre hablan entre sí. Por lo tanto, se toman a los demás por sorpresa, algo que deberían hacer si quieren competir. Creo que un buen ejemplo de ello es Apple, que acaba de anunciar una serie de nuevos iPhones con un diseño realmente asombroso, pero que se ha quedado un poco rezagada con respecto a Samsung, que está impulsando el 5G a un ritmo mucho más rápido de lo que nadie pensaba. De repente, todo podría cambiar en los próximos 12 meses en ese extremo del espectro. Esto dificulta las previsiones, porque los grandes fabricantes de equipos originales, como debe ser, se guardan muy en secreto los principales datos que podrían ser de gran ayuda.
Martin: Puedo verlo, sobre todo en algunos de sus productos de consumo. Sin embargo, la mayoría de los productos con los que trabajamos son más industriales. Suelen tener más visibilidad de previsión. La mayoría no son tecnología punta. El sector de los teléfonos móviles impulsa el mercado de componentes. Dondequiera que vayan, allí es donde el resto de nosotros acabamos yendo también. Pero el resto de los clientes -los de la base industrial- suelen tener mucha más visibilidad o previsibilidad que los últimos diseños. La mayoría de ellos no son diseños revolucionarios. Son mejoras de lo que ya ofrecían.
Matties: ¿Dónde se encuentra?
Martin: Me encuentro físicamente en Tampa, Florida. Trabajo a distancia y viajo.
Matties: Bien por ti. Somos una empresa virtual también, así que tenemos gente en la llamada de todas partes del mundo en este momento.
Martin: Agradezco toda la atención que estamos recibiendo, y espero que les resulte útil.
Matties: Mucho. ¿Hay algo de lo que no hayamos hablado y que crea que deberíamos tratar?
Martin: Como he dicho, estamos luchando contra las cuestiones arancelarias. Estamos esperando principalmente a que los fabricantes se muevan. Creo que va a haber un gran movimiento de negocios fuera de China a otras regiones para mitigar los aranceles. Todavía no ha tenido un gran impacto, pero creo que está al caer. Creo que va a tener un impacto significativo en unos meses. Ahora mismo, los distribuidores se han portado muy bien. Están absorbiendo lo que no pueden mitigar para nosotros, así que va a tener un gran impacto con los fabricantes sobre lo que eligen diseñar y qué productos compramos. Eso se nos viene encima. Y luego, en 2019, creo que el plazo de entrega de los MLCC de mayor tamaño va a ser más largo de lo que es ahora. Eso va a ser un gran problema.
Matties: No es sólo la capacidad de fabricación, es en realidad una escasez de los equipos para producirlos. Tampoco hay equipos suficientes.
Martin: Sí. Este junio estuve en Vishay, en China, y me dijeron que tenían equipos encargados desde hacía un año y que los habían pospuesto porque el fabricante no podía conseguir piezas.
Matties: Es un problema más profundo de la cadena de suministro, que va más allá del espacio.
Martin: Exactamente. Los fabricantes no pueden conseguir las máquinas para hacer más piezas porque los fabricantes de máquinas no pueden conseguir las piezas.
Matties: Muchas gracias, Stephanie. Ha sido muy informativo.
Martin: Gracias.